BENEFITS
Making logistics and inventory more efficient
Streamlining the maintenance process
Improving skier safety
Reducing human error
Ottimizing the inventory, maintenance, and management process of protective nets to ensure skier safety is one of the main challenges that a manufacturer and installer of safety nets must face and overcome. To achieve this goal, an advanced system that interacts with RFID technology has been implemented.
How has it implemented?
The UHF Tag Cable Tie, in the form of a high-quality waterproof ABS cable tie, has been specially selected for specific characteristics: ease of application to the nets and consequent difficulty of removal, the long reading distance guaranteed by UHF frequencies, the durability that allows it to be used in outdoor environments and adverse conditions (such as those of ski slopes), and the unique code it is equipped with, through which all information related to each type of protection can be traced.
The tags are applied to the nets stored in the warehouse, and when the logistics staff moves within the facility to conduct the inventory, they are read by an RFID handheld device, enabling faster and more efficient verification by signaling any errors or shortages. When the company is requested to cover a specific mileage of the ski slope with its nets, these are transferred from the warehouse to the race course. As the protections leave the warehouse, they pass through a UHF RFID gate that signals their exit by remote information transmission, ensuring that once they return, no discrepancies are detected between what has left and what has re-entered.
After recognizing the usefulness of RFID technology for logistics and inventory, the client decided to use Cable Tie Tags for the maintenance of the nets as well. For this operation, the staff uses specific devices to inspect the protections, automatically recording the information and transmitting it in real-time to the management system. This allows for monitoring the condition of the nets, planning maintenance interventions, and responding quickly to any issues.
The implementation of RFID technology has thus made the management of logistics and inventory more efficient, increasing the accuracy of verifications and reducing both execution times and human errors. Moreover, with this system, it has been possible to improve the traceability of the maintenance activities of the nets, facilitating their planning and consequently ensuring the safety of skiers.
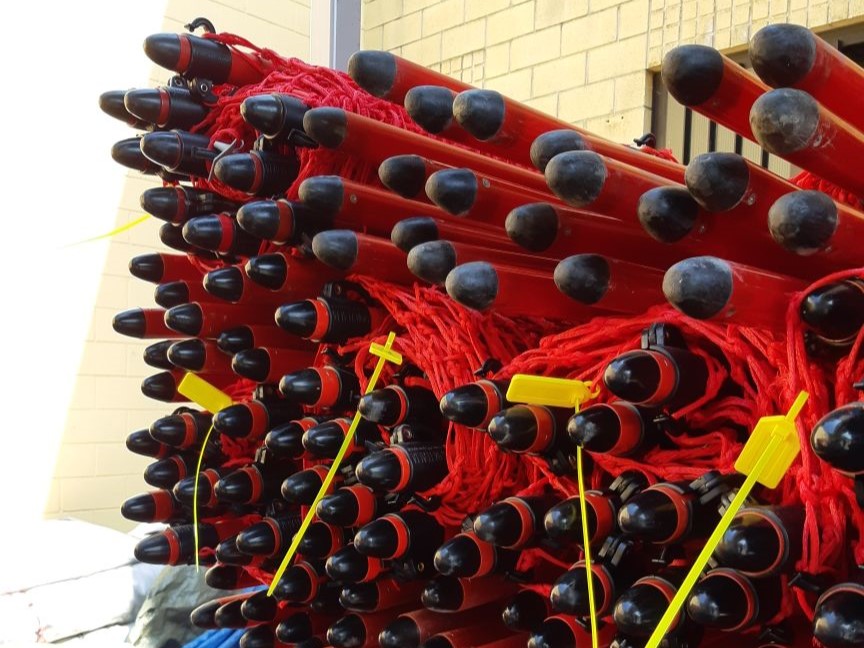
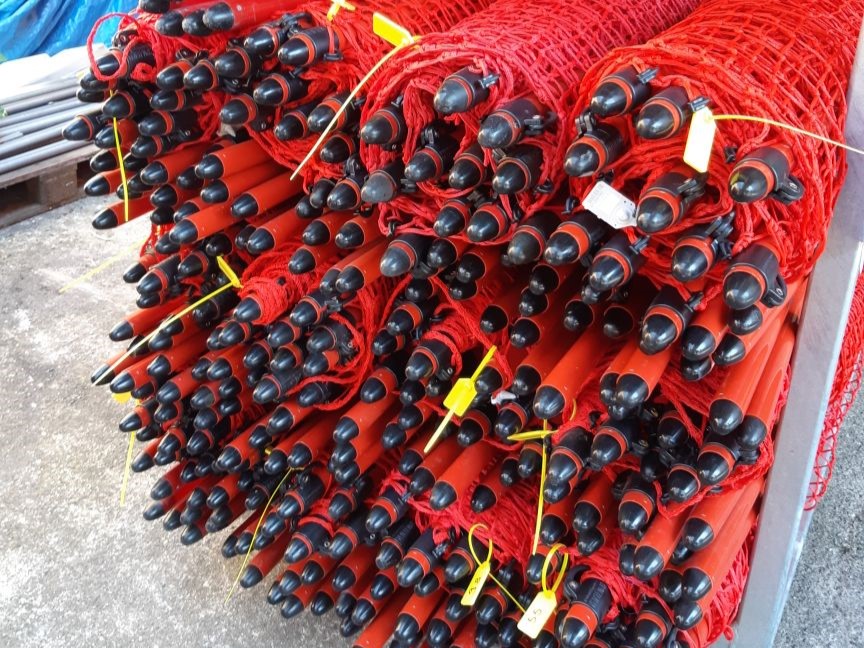
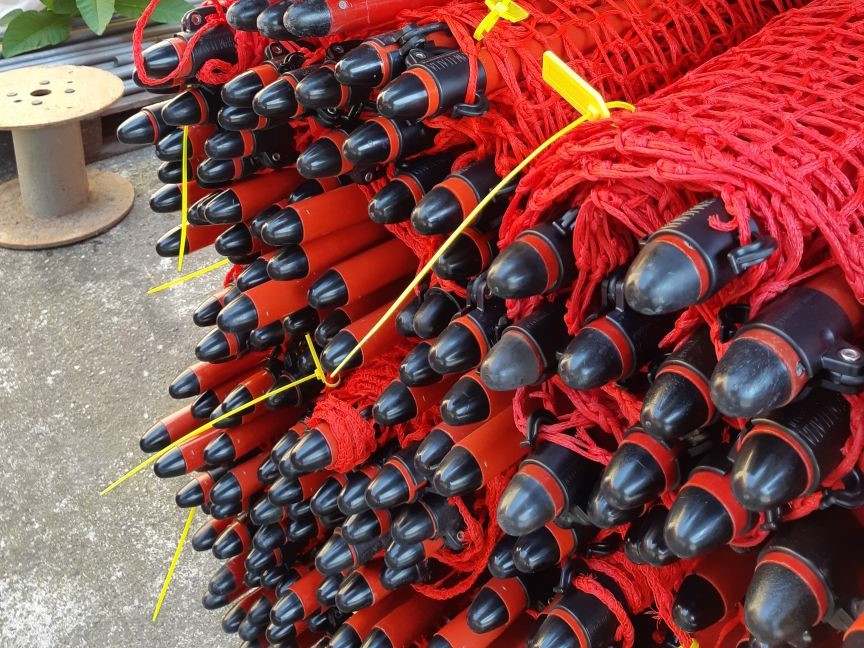
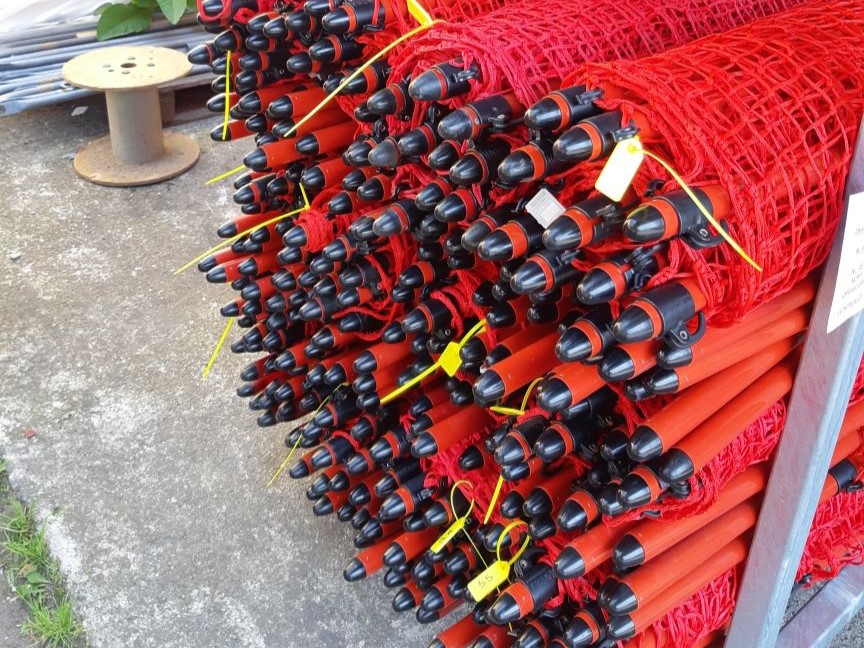
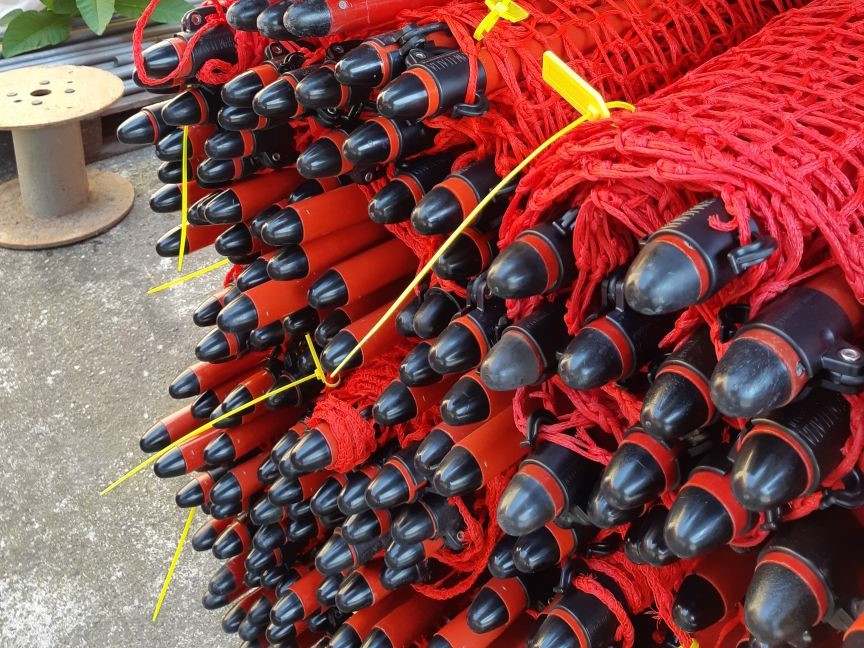